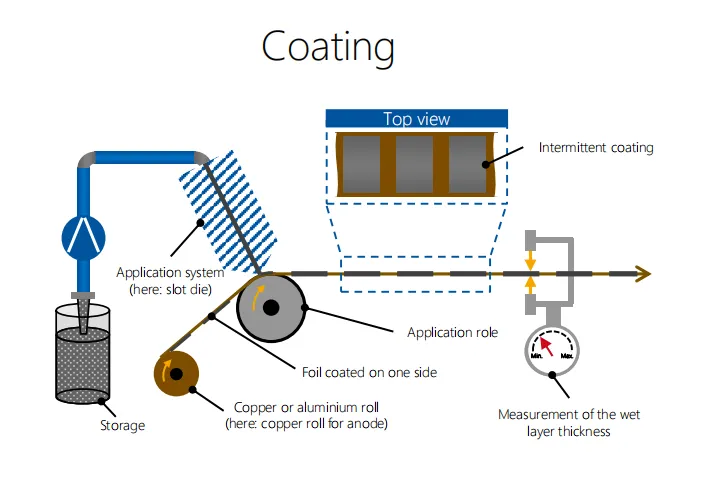
The main purpose of coating is to evenly coat the slurry with good stability, good viscosity and good fluidity on the surface of copper foil or aluminum foil. Its significance to lithium batteries is mainly reflected in three aspects: consistency, cycle life, and safety. During the coating process, if the thickness of the positive and negative slurry coatings in the front, middle and rear positions of the electrode sheet is inconsistent, or the parameters of the front and rear electrode sheets are inconsistent, it is easy to cause the battery capacity to be too low or too high. And lithium ions may be precipitated during the battery cycle, affecting battery life. During the coating process, it is necessary to strictly ensure that no particles, sundries, dust, etc. are mixed into the electrode sheet. If sundries are mixed, it will cause a micro-short circuit inside the battery, and in severe cases, the battery will catch fire and explode. Therefore, in order to make the winding process in the middle section as uniform and tight as possible, the coating error of the positive and negative electrodes is required to be as small as possible. The advanced level of the coating machine will directly affect the chemical performance of the battery and the yield of the final product. (Battery manufacturers usually require more than 99%).
The coating machine is the core equipment of the front-end process. Coating machines have experienced the evolution of three structural types, followed by scraper, transfer, and slit extrusion coating. The scraper type is mainly used in laboratory conditions; the transfer coating is mainly used in the production of 3C batteries; the slit extrusion coating is mainly used in power batteries, and this type has increased rapidly due to the explosion of power battery production demand in recent years . The slit extrusion coating technology, as the most advanced technology among the three, can be used for higher viscosity fluid coating to obtain higher precision coating. From the perspective of the structure of the coating machine, the design of the coating head has an extremely important impact on the coating accuracy.
The technological advancement of coating machine equipment mainly examines four aspects: coating technology, tension technology, deviation correction technology, and drying technology. Coating technology needs to meet the production requirements of different thicknesses.
At present, the thickness of the positive lithium battery aluminum foil is as thin as 6-8 microns, the thickness of the negative lithium battery copper foil is as thin as 4.5-6 microns, the separator coating is only a few microns, and the graphene coating is even thinner. Different thicknesses also need to develop different coating methods for customers to ensure that the coating thickness accuracy of the slurry is controlled belowaspects: coating technology, tension technology, deviation correction technology, and drying technology. Coating technology needs to meet the production requirements of different thicknesses.
At present, the thickness of the positive lithium battery aluminum foil is as thin as 6-8 microns, the thickness of the negative lithium battery copper foil is as thin as 4.5-6 microns, the separator coating is only a few microns, and the graphene coating is even thinner. Different thicknesses also need to develop different coating methods for customers to ensure that the coating thickness accuracy of the slurry is controlled below 2 microns.