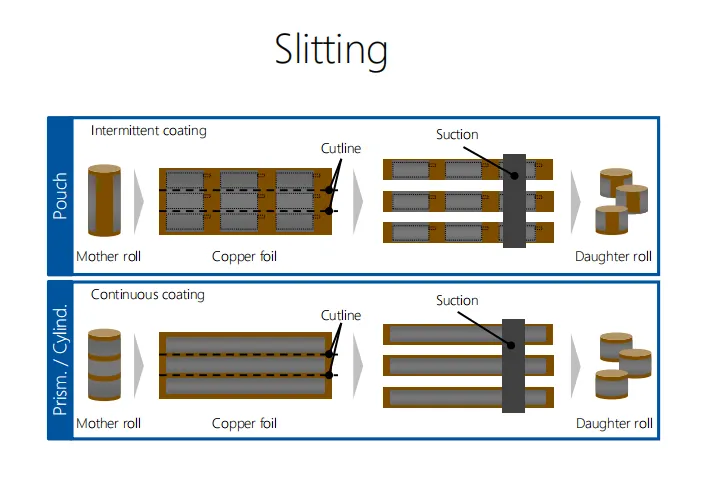
The function of the slitting machine is to slit the rolled electrode sheet to the required width, which is the key process before winding. The low-end slitting machine has low mechanical precision and simple tension control, which cannot adapt to the slitting of ultra-thin film materials. With the improvement of users’ requirements for slitting efficiency and slitting quality, high-end slitting machines gradually have the function of wavy edge slitting, and have better tension control technology to optimize slitting speed and slitting quality. At present, the high-end cutting speed in China has exceeded 70 m/s.
The main technical difficulty in the electrode sheet slitting process lies in the treatment of burrs, wavy edges and powder falling. Burrs, especially metal burrs, are very harmful to lithium batteries. Larger metal burrs directly pierce the separator, resulting in a short circuit between the positive and negative electrodes. The electrode sheet cutting process is the main process of burr generation in the lithium-ion battery manufacturing process. Generally, the burrs are required to be below 12 microns. Wavy edges and powder falling are also defects. When wavy edges appear, edge correction and vibration will occur when the electrode sheet is cut and wound, thereby reducing the process accuracy. In addition, it will also have a negative impact on the final thickness and shape of the battery. The powder loss of the electrode sheet will affect the performance of the battery. When the positive electrode powder falls, the battery capacity will decrease, and when the negative electrode powder falls, the negative electrode cannot wrap the positive electrode, which will easily cause lithium precipitation.