Since the reform and opening up, China’s manufacturing industry has developed rapidly and rapidly promoted the process of industrialization. The development of China’s manufacturing industry is closely related to the process of industrialization and the process of economic globalization. China has given full play to its comparative advantages and actively participated in the division of labor in the global manufacturing value chain. While promoting the development and industrialization of its own manufacturing industry, it also contributes to the world economy Growth and the process of economic globalization have made their contribution. In the production process of electronic products,the accessories placement technology has changed from the original labor-intensive manual + traditional equipment production process to the relatively flexible and better robot assembly method, which is gradually being replaced by a technology-intensive automatic mounting system. The emergence of fully automatic high-precision auxiliary material placement equipment has fundamentally changed the traditional production and operation methods of auxiliary material placement.
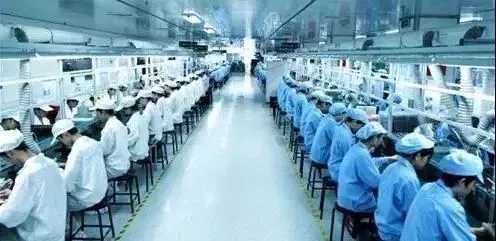
Manual work
The process of product assembly is decomposed according to the operation process. Due to the difficulty of the product process, the time spent is also inconsistent.In order to ensure the maximum efficiency of the production cycle, engineers need to design each process of the product reasonably for easy realization, some can be assembled directly, and the positions with high precision requirements need to be assembled manually by matching semi-automatic equipment. Due to the influence of the production speed, some processes are performed by a single operator, and some processes are performed by multiple operators.
Features of manual work
- Low production capacity, relying on the proficiency of employees
- Difficult recruitment and management
- The quality of manual placement is unstable
- The accuracy of manual placement is low
- High comprehensive cost
Traditional ring line operation
The product is placed in the conveying carrier (the carrier is generally a one-out-two structure), and it is transported to the designated position through the belt conveyor. After the machine receives the signal that the carrier has arrived at the work area, the equipment positioning mechanism drives the product positioning fixture to carry out the loading. The product in the tool is positioned, the robot arm attaches the grasped auxiliary materials to the product, the equipment positioning mechanism returns to the origin, and the conveying vehicle transports the product to the next process after receiving the signal, until all processes are completed in sequence
Ring line features
- Adopt ring belt track line, which can integrate screw machine, detection and other processes.
- The guarantee of product placement accuracy depends entirely on the processing accuracy of die-cutting accessories and fixtures.
- The requirements for the incoming auxiliary materials are very high. The error of XYW three directions cannot exceed 0.1mm, and the coil material cannot leak material, so the comprehensive cost of changing the sheet material to the coil material increases by more than 30%.
- The positioning fixture is dedicated to the special machine, and the whole set of positioning fixture and suction nozzle needs to be replaced when changing the model, and the use cost is high.
- It takes a long time to change the new and old products, because this type of model has many adjustment positions, and all adjustment positions are completely dependent on the experience of the operator.
- Engineering capability: The equipment accuracy is average, and it can only meet the placement accuracy of products with a placement accuracy of ≥±0.3mm, and there is a defect rate of 5%±2%, and the machine attachment of embedded accessories is basically impossible.
Arm placement machine operation
The arm placement machine has high flexibility in use, so there are two kinds of highly integrated applications with a vision system and more traditional implementation methods without a vision system in the application of the arm placement machine. Among them, the application without a vision system The processing method is basically similar to that of the circular line. Compared with the circular line equipment, the cost of the arm mounting structure is higher, but the flexibility is better than that of the circular line, the final choice of whether to have a vision system depends on the product requirements of the end user. The most commonly used are four-axis robots, mainly EPSON and YAMAHA are the most widely used.
Arm placement machine features (with vision system)
- Good flexibility and strong adaptability, which can satisfy the whole production process from loading, machine sticking and unloading
- Stable performance, low failure rate and low maintenance cost
- The cost of auxiliary materials is lower than that of the circular line, and the price of the whole set of auxiliary materials according to the model is basically the same as that of manual auxiliary materials
- The fixture is dedicated to the special machine, and the whole set of positioning fixture and suction nozzle needs to be replaced when changing the model, and the use cost is high
- The head can be equipped with 1-4 suction nozzles of different specifications, and the placement accuracy of ≤±0.025mm can be achieved through the visual positioning system
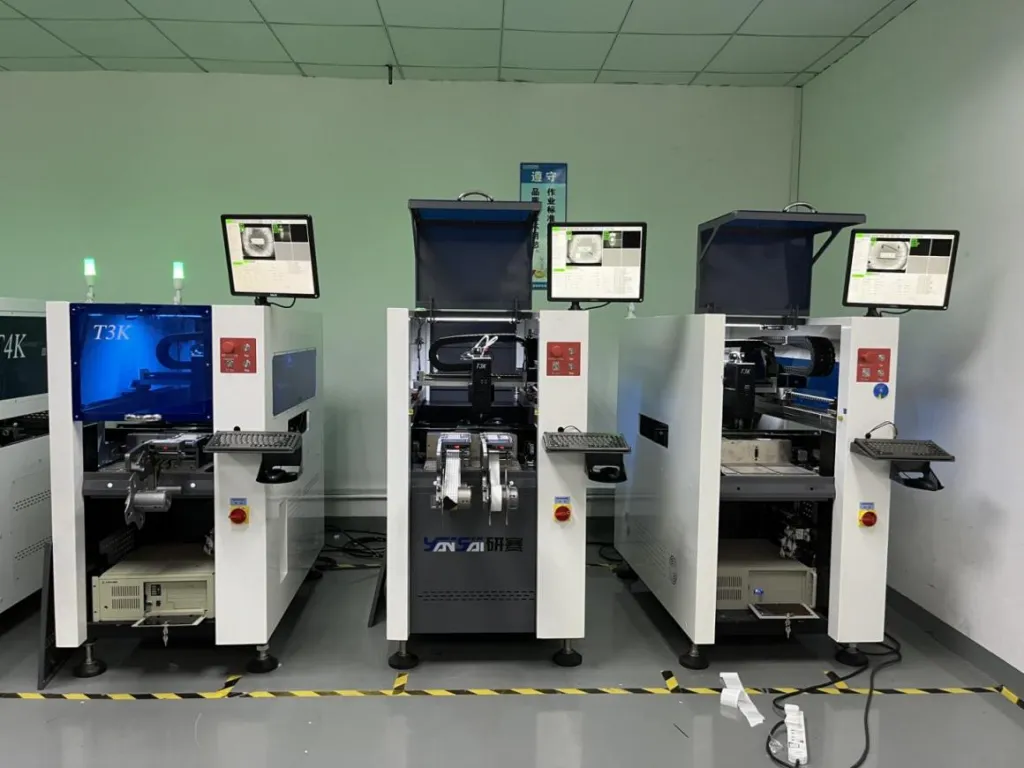
High-precision mounting line
The fully automatic high-precision mounting machine is to accurately and stably grab and place the auxiliary materials on the designated position on the attached product by moving the placement head to achieve high-speed and high-precision placement. Shenzhen Taipu Automation Equipment Co., Ltd. latest the first-generation high-precision placement machine adopts a modular design, which can freely match the number and type of machines according to the requirements of the process, so as to minimize the cost of use for customers and improve the production efficiency and accuracy of placement.
Features of High Precision Mounting Line
- Accurate identification and positioning system: The fully automatic high-precision placement line has a self-developed accurate image identification and positioning system. value, MARK point, right angle and other feature recognition to mount different products, and use a professional vision system to perform positioning and analysis throughout the process to reduce the occurrence of errors.
- Cost of use: In terms of auxiliary materials, it can be compatible with multi-row or single-row methods, and can reduce the cost of auxiliary materials in terms of defects in auxiliary materials, shortage of incoming materials, and position accuracy of auxiliary materials.
- Fool-proof function: the visual software can identify the poor placement caused by irregular feeding, and prevent the outflow of unqualified products and bad products to the greatest extent.
- Versatility: The whole machine adopts modular and standardized design, the track adopts international standard design, and can be connected with international standard design products at will. Feida (independent research and development) has an independent operating system and can be used with other equipment at will. Fixtures Designed in a universal way, it can perform functions such as automatic adjustment according to product specifications.
- Safety: The whole line adopts a closed-loop control system, and there are safety protection devices for each line, feeding and discharging positions, and the whole machine is designed in strict accordance with the requirements of national laws and regulations.
- Storage: The main machine adopts industrial computer, which can be stored according to the requirements of use. For products with existing production records, only need to call out the original documents to produce quickly. When the equipment stops running due to external factors, it only needs to be replaced The stored production data can be called out again, reducing the debugging man-hours caused by the loss of the program.
Requirements for accessories
- Artificial mounting accessories Features of artificial mounting accessories.
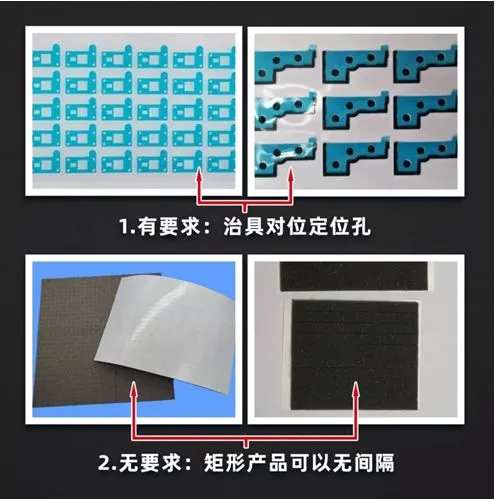
- Incoming material method: Flake incoming material.
- Incoming materials with position accuracy requirements: do positioning hole die-cutting at the hollowed out position of the product, and align and fit with the jig during manual work.
- Requirements for low position accuracy: In order to reduce the cost of auxiliary materials, the die-cutting process generally adopts a design without intervals, which is mainly reflected in rectangular products.
- The requirements for die-cutting processing technology are relatively low, the process flexibility is relatively strong, the cost of die-cut products with positioning holes is relatively high, the waste is relatively large (it is more obvious when laminating products with multiple modes at the same time), and the overall auxiliary material cost is low.
- Ring line accessoriesFeatures of ring line accessories.
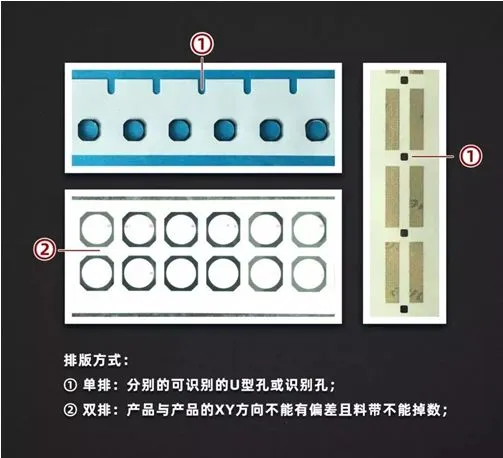
- According to the size of auxiliary materials, roll material typesetting generally adopts single row or two rows of incoming materials.
- There are strict requirements on the distance between products and the relative position, and the distance between products and sides (die-cutting pain point 1).
- Leakage and lack of materials will increase the throwing rate of the equipment. The single-row typesetting method does not affect it. The double-row method needs to be thrown away as long as one of the auxiliary materials is missing (limited by the mounting method, die-cutting pain points 2).
- Since it can only accept single-row or double-row incoming materials, the cost of using die-cutting equipment is very high. Taking single-row as an example, if eight auxiliary materials can be produced at one time, the processing quantity of 1H of die-cutting equipment will be single-row 8 times.
3. Arm placement machine accessories
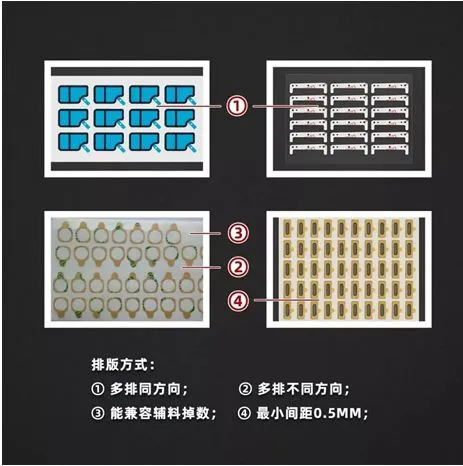
Features of auxiliary materials for arm placement machine
- Compatible with the layout of the above-mentioned auxiliary materials with spacing.
- Compatible with single-column and multi-row typesetting, the typesetting is more flexible, and the minimum distance between products can be reduced to 0.5mm, it needs to be combined with the difficulty of product technology.
- It is more flexible for the typesetting of auxiliary materials, and can realize multi-row and multi-directional arrangement.
Advantages of TaiPu surface mounting machine
Scope of application:
Products that require mounting accessories include mobile phone middle frames, mobile phone battery back covers, notebook computers, smart wearable devices, navigators, FPC, PCBA, precision stamping parts, and injection molding parts (including micro-curved surfaces), etc. The auxiliary materials that can be mounted include insulating adhesive, double-sided adhesive, conductive foam, conductive adhesive, conductive cloth, high temperature adhesive, conductive copper foil, PET sheet, SUS reinforcing sheet, graphite sheet, etc.
Equipment advantage
- High site utilization rate: The equipment is compact and reasonable in design and occupies less land, saving the cost of plant rental. Dimensions: L766W890H1500mm, already the narrowest in the industry.
- Flexible machine combination and high machine utilization rate: single module design can freely and flexibly combine machines according to customer product requirements.
- Intelligent recognition: CCD vision, optical fiber sensor positioning and recognition, no need for fixtures, greatly reducing specific expenses such as design, production, storage, management, etc., effectively preventing re-posting and missed mounting.
- High production capacity: the current production capacity of the whole line reaches 1200PCS/H, and a single placement takes 1.0-1.5s/piece of auxiliary material.
- Strong compatibility and high site utilization rate: double-head mounting, two different or the same auxiliary materials can be attached at the same time.
- Fast model change: using industrial computer control, program integration, plug-in feeder for fast material change, easy operation, off-line debugging and maintenance can be done, and day and night shifts can be used to produce different models of products.
- Self-contained MES data integration: visually read the QR code, upload data, and effectively trace the source of information management.
- High product yield rate: Belt transmission has its own guiding mechanism, and the optical fiber senses the docking position, which effectively reduces product collisions, does not jam machines or materials, and reduces damage and scrapped products.
- High placement accuracy (±0.05mm): The XY axis transmission of the machine is integrally formed by mold opening and casting, with compact structure, small deformation, high precision and long service life.
The high-precision intelligent mounting machine has low requirements on auxiliary materials and strong applicability. It can meet the high-precision mounting requirements of various tiny products and micro-curved products. It is a perfect device for electronic product assembly plants to reduce labor and increase efficiency.